In 2016, the National Oilheat Research Alliance (NORA), in collaboration with the New York Oil Heating Association (NYOHA) and Oil Heat Comfort Corp., opened a research and training facility the—NORA Research & Education Center, in Plainview, NY, under the direction of Dr. Thomas Butcher.
Indoor Comfort Marketing’s publisher, Don Farrell, spoke to Dr. Butcher about the lab, its funding, its staffing, its projects and its goals.
Don Farrell: What is the official name of the research center and what is its mission?
Tom Butcher: The official name is NORA Research & Education Center. The mission of the research part is to support the development of advanced technologies that lead to improved efficiency, increased integration of renewable fuels and enhanced reliability of liquid fuels heating systems. Liquid fuels are traditional petroleum-based fuels and also biofuels such as biodiesel and other wood-derived liquid fuels.
DF: Why choose Long Island for the location?
TB: Long Island, NY is an area that’s very strong for heating oil, which is important. Many stakeholders and local industry people who really care come frequently, which is fantastic in helping with the lab.
The access to transportation is great, between major highways and air travel. In addition, it’s close to major universities, and of course, Brookhaven National Laboratories, with whom we have had the opportunity to collaborate.
DF: Oil Heat Comfort Corp. and New York Oil Heating Association (NYOHA) are two stakeholders as well, correct?
TB: Right, but their involvement is more in the technical training/education functions.
DF: How is this lab funded?
TB: NORA has a mandate in its statute that a minimum of 30% of its budget is spent on Research and Demonstration; this is a major source of funds. Additionallly, the New York State Energy Research & Development Authority (NYSERDA) is also providing funds for specific projects now and certainly we’re hoping to make that a continuing part of this. NORA mostly funds the day-to-day operations while NYSERDA cooperates by funding projects.
DF: What about when you collaborate on joint projects with manufacturers?
TB: W are not opposed to the idea of some funds coming in from manufacturers. What could work is that manufacturers could go to a third party—like Department of Energy (DOE) or somebody else—with a package proposal with some funds for the NORA lab, which would then come through the company. Certainly, it could make a lot of sense for the NORA lab to cooperate with manufacturers on research projects as part of a team, in which case the funding would be external—it could be a company or a third party.
DF: Who staffs the research center?
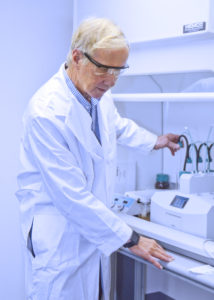
Dr. Butcher
TB: It is staffed by me and two interns from Stony Brook University. I have a PhD in research engineering with well over 30 years of experience in combustion research.
Jonathan McCutcheon, who goes by the name of “Mike,” is a senior, graduating in May, from the Chemical Engineering program at Stony Brook University. He has a great deal of experience in the biofuels lab at Stony Brook, which is we consider to be a partner institution for us. He has a lot of personal interest and experience with biofuels—he’s very strong with analytical techniques for biofuel characterization. He will graduate with a Bachelors in Chemical Engineering.
Brian Gainey is a Mechanical Engineer. He is also going to graduate from Stony Brook University in May. He works very closely with the engines combustion lab at the Advanced Energy Research & Technology Center at Stony Brook. We have a very good working relationship with that team as well. He has been accepted into the PhD program at Stony Brook with a fellowship. We hope to have some continued involvement with him.
DF: Do you have any plans for additional staffing at this point?
TB: Not at this point. Things are going so well with the current intern program that we are inclined to keep going with that—if not with the current interns, then with the next group. We may want to eventually add a permanent staff, but we will see.
DF: When did the lab open, is it fully-equipped with everything you need and what kind of equipment do you have?
TB: The lab opened about a year ago (April 2016). I would say we have ramped up to the first level we wanted to get to and now we are going to be more strategic in adding new instrumentation as we feel it’s useful and necessary. In regards to the kind of equipment we have, I divide that world into two parts. One is fuel quality and composition and the other is combustion.
On the combustion side, we have a first class gas analyzer, infrared for carbon dioxide, carbon monoxide, sulfur dioxide and nitrogen oxide analysis. It is complete with a full-up sample conditions system, which is really important—it does the pumping, filtering, drying, the metering and cal gas, we’re all set up on that. We have an outstanding data acquisition system that can measure all the parameters, temperatures and voltages, then process and display them on a screen as well as log them. It’s a highly programmable system that can not only measure everything we need to do, but also control things. For example, if we want to have a hot water load on a boiler that turns on and off according to some program schedule, we can do that with our current data acquisition system. We’ve got sensors everywhere and control valves that are computer controlled. I’m really feeling confident that we’ve got the tools we need to do a lot of great measurements.

Biodiesel content tester
Fuel quality is increasingly important. We’ve been doing a lot of field studies. We have been sending samples out to a lab in the Midwest for analysis. However, we recognized early on that we need to build up the analytical chemistry capability within the lab and we have been doing that deliberately, thoughtfully and slowly to ensure that we are making the right investments in the right instruments. Right now,we have centrifuge so we can see what’s on the bottom of oil samples, such as water particulates. We’ve got a biodiesel content tester, a biodiesel blend acid number measurement system and we have the Rancimat tester for oxidative stability of biodiesel blends.
DF: Now that you have all of this great equipment and good help, what are the projects you are currently working on?
TB: Let me start with the combustion—we’re now launching into a study of CAD cell resistance with different biodiesel blends to discover if there are varying combustion characteristics of different biodiesel blends as well as CAD cell response.
We are completing testing under the tankless coil project to evaluate the performance of current and future tankless coils and develop best practices in a quantitative way based on laboratory measurement on how to get the best efficiency from tankless coil systems. We are doing a lot of idle-loss and efficiency measurements for different heating systems. We are testing novel burners and systems that are being developed as part of the NORA research program; for example, the Babington burner, Novatio burners, etc.
On the fuel quality side, we have been carrying out a field sampling program, very formally organized and very carefully planned. We are finding that fuel quality research needs to continue because we are still seeing concerns in the field. Many service organizations are interested in better understanding the fuel quality that they are dealing with. We don’t have all the measurements yet, but at least we think we have the most important basic ones. We are able to essentially complete a health check on the fuels that are out in the field on a quick turnaround basis.
We are being approached by heating oil marketers with a range of concerns about their fuel quality in the field. To whatever degree we can, we are assisting with our analytical capabilities to help them understand what they’re dealing with and to help them develop solutions for those problems. That includes water in fuels, blocking filters, excessive degradation rates for fuels, pump problems such as sticking and seal leaks—which we are seeing on an isolated basis—and nozzle fouling. These have been problems that are rather common in the industry, and have been for a long time. We are doing whatever we can do to help address any unusually high occurrences of such problems.
DF: Are there any projects or any areas that you’d like to tackle that aren’t yet on the docket?
TB: Right now the focus is expanding our fuel quality analysis capabilities. I think that we have room to improve in that area. We are finding, in our first year of experience, that this is an area where we can really make a contribution to the industry, by having those capabilities locally and giving us the ability to really dig in on local and regional problems. I’d like to measure particulates, study long term storage stability, fuel blending and more.
DF: Are the lab services available on a contract basis to third parties?
TB: We are evaluating that question. Part of the reason for wanting to have a situation where an outside company can contract to use the lab services is that, when we do that, we can guarantee them confidentiality of data flow— because they own the data, they basically paid for it. It is a little unfair for NORA to pay for research that doesn’t benefit the entire industry and we are really sensitive to that, so if it’s something that benefits one company and helps promote their business, then it’s only fair that the cost of that should be borne by the company it is benefitting. So, because NORA is funded by the industry-at-large, all the work NORA does should go into the public domain; but if a manufacturer wants something that is specific and remains proprietary, they will then have to pay for that service separate from the general NORA funding. ICM